Welding the hull is a big job and it can makes or break a steel boat. I followed the recommended books of G.Klingel and T.Colvin. Correspondence with Nick Skeates and the TAFE night welding course also were invaluable. Prior to full hull seam weld up, the entire hull is held together by tack welds at about 6" spacings. Full weld up begins on the outside. Once outside welding is done then the hull is rolled over for internal welding.
Good preparation of the weld seam is important. Beveling the plate edges and leaving a 1mm gap between plates/chine bars allows for good weld penetration and also stronger weld with no hairline cracking due to shrinkage (could occur if the plates are hard-pressed together)
3.2mm weld rod stubs were used as spacers between frames and chine bars or stringers (These were fitted at the framing stage befoe hull plating). They were knocked out as seam welding progressed past them and the hull began shrinking. In retrospet 5mm spacers would have been better, especially near frames 1 and 2 in the bow, where hull shrinkage was greater.
I used short weld runs around 2-4" long. The short welds are needed to prevent any unsightly distortion (buckling) of the plates occuring. After doing a short weld i moved to another location to allow the first weld time to cool down. Both sides of the hull are also welded symetrically to prevent the hull pulling out of shape. Full hull welding has the effect of shrinking the hulls size by about 5-10mm.
A welding pattern needs to be followed. This is to balance out all the shrinkage forces evenly. I began near the center of the hull in the garboards (keel meets hull joins) and worked outwards towards the ends of the hull. After several meters of weld were in the garboards, i started on the lower chines..when several meters were on the lower chines , i started on the upper chines.
When a longitudinal (sub-horrizontal) weld seam reached a tranverse (up and down) plate join then i started welding down the plate join. Small plate bolts and washers were knocked out before the weld seam reached them, otherwise they would be clamped in by hull shrinkage.
After a weld was done the slag is chipped off with a welders hammer and wirebrushed. Then the angle grinder was used to prepare the end of the first welds to meet the next weld. If a pinhole was noticed, it was ground out and rewelded.
Power wire brush fitted to 4" angle grinder make weld cleaning fast and easier. A face sheild is needed to protect eyes from any wires that may fly off.
The soft chines of the wylo2 are a bit unusual. They are 2" flat bar laid flat which forms the hull skin and makes a gentler corner which helps give the apperance of being a rolled plate hull instead of a hard chine hull. But the problem i noticed during weld up is this is easier to distort than usual chine methods of a solid round rod or on-edge chine bar. So i tack welded tempoary 1" flat bars on edge, on the outside, in the center of each 2" chine bar to prevent chine distortion (photo above).
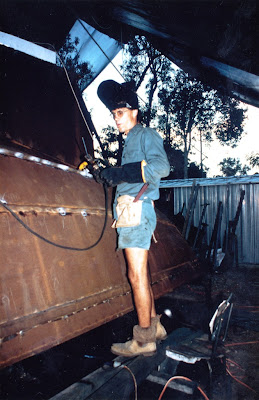
Welding seams. The rubrail was added prior to weld up. It is a 40x20mm steel channel set about 6" below (above in this pic) the gunwale. It acts as a very strong double external hull stringer. As designed, it is also more aesthetic, reducing any slab-sided effect of the topside plates.
Some builders make the rubrail coincident with the gunwale (Klingel-Colvin method) fitting a 40-50mm preferably galvanised pipe instead of the designs 1" flat bar gunwale. This then requires an extra internal 1" flat bar stringer to be fitted to maintain hull stiffness around where the design rubrail would have been. A gunwale rubrail takes all the bumps well but it does make the hull appear to be a bit stockier aesthetically than the wylo2 design rubrail method.
I did the hulls chines and garboards with a traditional 180 amp stick welder with 3.2mm rods and about 110-130 amps set. It takes 15 amp AC input. The 3mm hull plate joins needed 2.5mm rods with ~90 amps set. It may be better to "back-step" these joins, weld upwards starting 2" down from the previous weld.
Arond this stage i bought a 130 amp MIG (metal inert gas) welder with 10 amp AC input for thin 3mm hull plates. It produced far less distortion than the better-penetrating 180 amp stick welder. The MIG was set at around 90-110 amps and a continuous wire feed from a spool activated by a trigger is easier to weld too. The MIG can be run gasless with flux coated wire or with an Nitrogen bottle attached by regulator and hose. The inert nitrogen gas of the MIG makes a gas sheild over the molten weld keeping out oxygen and making for a good weld without slag etc. My MIG prefered downhand welding (weld gun above weld). On overhead welds the MIGs gas sheild cowl got quickly filled up with weld spatter, never a problem with the arc welder.
The MIG has a big box, almost the same size as the arc welder, but with only 8 feet of flexible cable to the weld gun (no "traveller" as in expensive MIG welders). so moving the MIG with nitrogen bottle around was more difficult than the simpler 180amp arc welder with its long 10m cable. For me the MIGs welding advantages for 3mm plate outweighed its mobility disadvantages. (It wasn't powerfull enough for the thicker plates or chines so both welders were good for their particular uses)